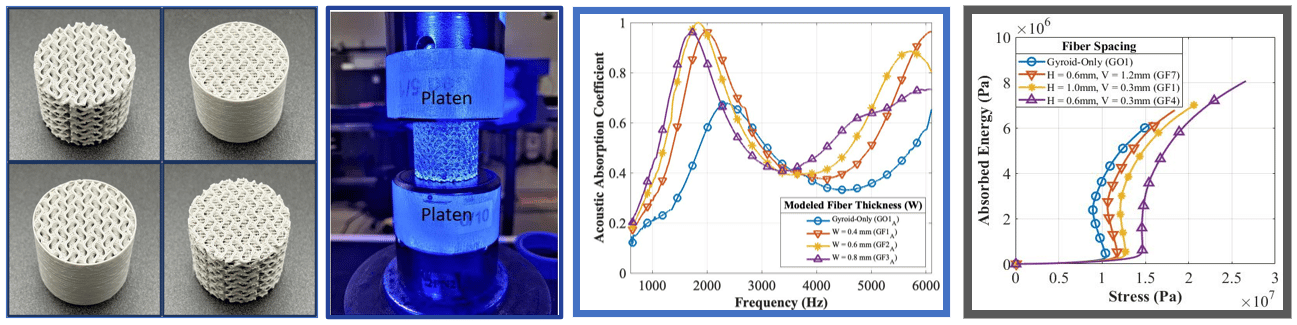
While decreasing structural pore size leads to enhanced mechanical and acoustical properties, the added weight and flow disruptions limit its applications and reduce the mechanical energy absorption performance. In this project, we introduce a method of decreasing the pore size without significantly increasing structural weight by adding a fibrous network to a porous architected cellular structure. The use of additive manufacturing enables the fabrication of these complex geometries. We study the effect of porous and fibrous parameters—including structural relative density and fiber thickness—on the structure’s acoustical, mechanical, and flow resistance properties. Our multifunctional structures offer effective sound absorption capabilities at low frequencies, with most samples approaching total absorption at approximately 2000 Hz, while showing improved energy absorption and mechanical stiffness, without any flow penalties.
Status: Current
Collaborators: Prof. Suresh Keshavanarayana (WSU), Spirit AeroSystems
Funding Agency: Lockheed Martin Space
Spatially Varying Architected Metal Foams with Novel Topologies
Architected structures obtain their properties not only from the base material but also from their underlying cellular architecture. Additive manufacturing (AM) enables the fabrication of complex architected structures; however, current AM technology has material and scalability limitations. In this project, we are collaborating with ERG Aerospace to design and fabricate architected metal foams with spatially varying pore structures that may be tuned to provide application-specific multifunctional performance. The project leverages our combined expertise in the design and understanding of architected structures and to make such structures using material systems currently incompatible with AM processes.
Status: Current
Collaborators: ERG Aerospace, Prof. Suresh Keshavanarayana (WSU)
Funding Agency: AFWERX
Additive Manufacturing of Multifunctional Ceramics for Aerospace Applications
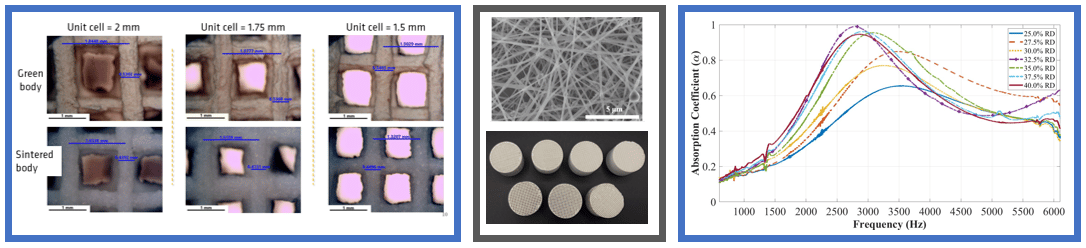
In this collaborative project, our goal is to enable the efficient AM of CMCs for multifunctional space and aircraft applications. We are systematically investigating the impact of various synthesis parameters on the AM process, synergistically developing scalable AM techniques for fabricating complex structural topologies, and evaluating the multifunctional response of the fabricated CMCs. The obtained insights will assist the rational design and fabrication of new multifunctional CMC components of high interest to NASA and US industry. The functionalities of primary interest are the thermal, mechanical, and acoustical response.
Status: Current
Collaborators: Prof. Wei Wei (WSU), Prof. Ted Adler (WSU), Prof. Dong Lin (Oregon State University), Spirit AeroSystems, National Institute of Aviation Research
Funding Agency: NASA, Spirit AeroSystems, National Institute of Aviation Research
In-Situ Process Monitoring of Additive Manufacturing Methods
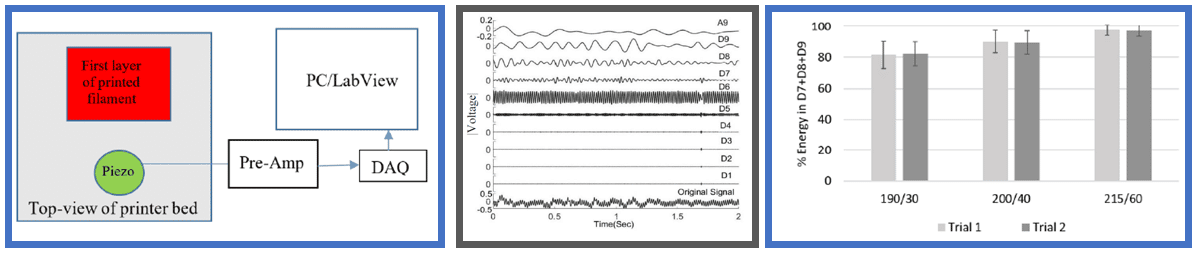
Additive manufacturing (AM) methods allow the fabrication of complex geometries without increasing the complexity of the manufacturing process. However, technical challenges associated with process repeatability and reliability make it difficult to ensure a final part quality without resorting to destructive test methods. Thus, effective in situ monitoring methods are necessary to encourage further adoption of AM methods for large volume part fabrication. In this project, we are exploring the possibility of using vibroacoustic emission monitoring for AM process failure detection. Vibroacoustic emission monitoring, in combination with wavelet and time-frequency analysis methods, allows early fault identification. The failure identification process may be automated by using machine intelligence algorithms such as K-means clustering. Developed automated process monitoring and failure identification tools will allow in situ monitoring and quality control for AM methods.
Status: Current
Collaborators: Dr. Vis Madhavan (WSU) and Dr. Wilfredo Moscoso-Kingsley (WSU)
Predictive Engineering Tools for Injection Molded Long Carbon-Fiber Thermoplastics
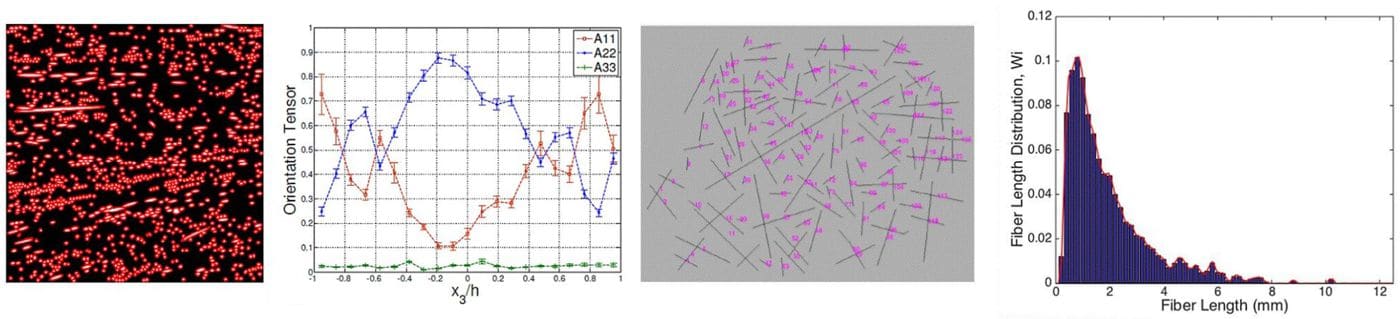
Long fiber thermoplastic composites offer many advantages for light materials and are finding increasing use in the automotive and aerospace industries. The local elastic properties of such materials are a function of fiber length and fiber orientation. Thus, predicting the fiber length distribution and fiber orientation distribution during injection molding of a component is critical for predicting the component elastic properties. Further, high precision experimental data are necessary to validate numerical predictive tools. In this collaborative effort, we developed a semi-automated fiber orientation and fiber length measurement tools for experimental verification of various numerical models. The tools utilize MATLAB to implement image processing routines and obtain stereological fiber orientation and fiber length distributions. The codes are available on request.
Status: Completed
Collaborators: Pacific Northwest National Lab., Autodesk Inc., Magna, Toyota, Plasticomp Inc., Prof. Mike Sangid (Purdue University), Prof. Charles Tucker III (UIUC)
Project Sponsors: Department of Energy
X-ray Tomography Characterization of Fiber Reinforced Polymer Composites
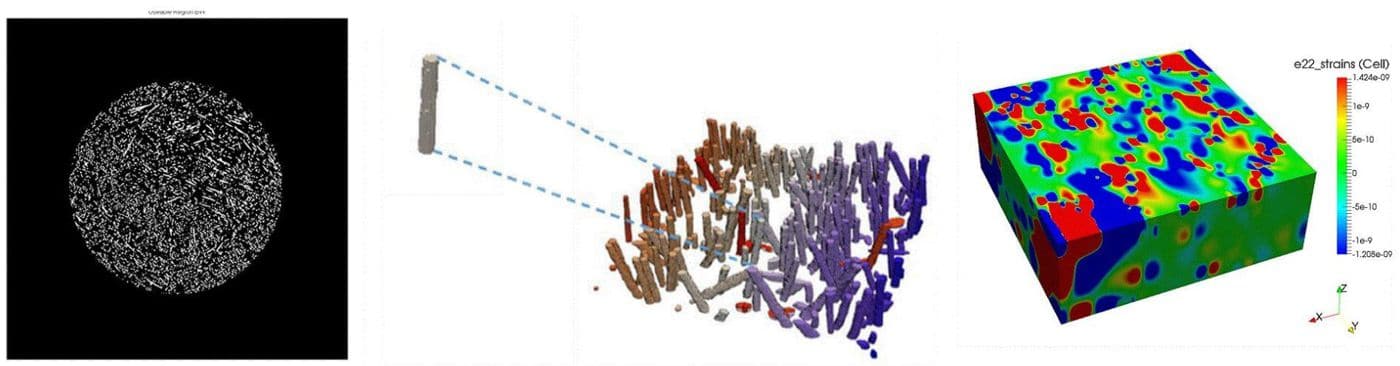
We use micro-tomography coupled with digital image processing to develop a data analysis framework, which hinges on a careful synergy between the two. Accurate measurement and analysis of material microstructure requires efficient means of separating and uniquely identifying the preferred microstructure from other constituents of the sample. Although there are several software capable of thresholding and segmentation, there are limits to user customization of these techniques. Motivated by this, we use the resources available under MATLAB’s Digital Image Processing Toolbox and a programmed metadata dependent correlation to develop an in-house MATLAB code to perform thresholding and segmentation on gray scale tomograms. These tools provide a platform to quantify the microstructure and fully understand its evolution with applied loading within SFRC’s currently being used extensively in the aerospace and the automotive industries. We use tomograms of glass fiber/polypropylene composites to demonstrate the method. However, this can be applied to characterize other short fiber reinforced polymer composites materials.
Status: Completed
Collaborators: Prof. Mike Sangid (Purdue University), Ronald Agyei (Purdue University), Xianghui Xiao (APS Argonne National Lab)
In situ Study of Mechanics of Sedimentary Rock Cutting
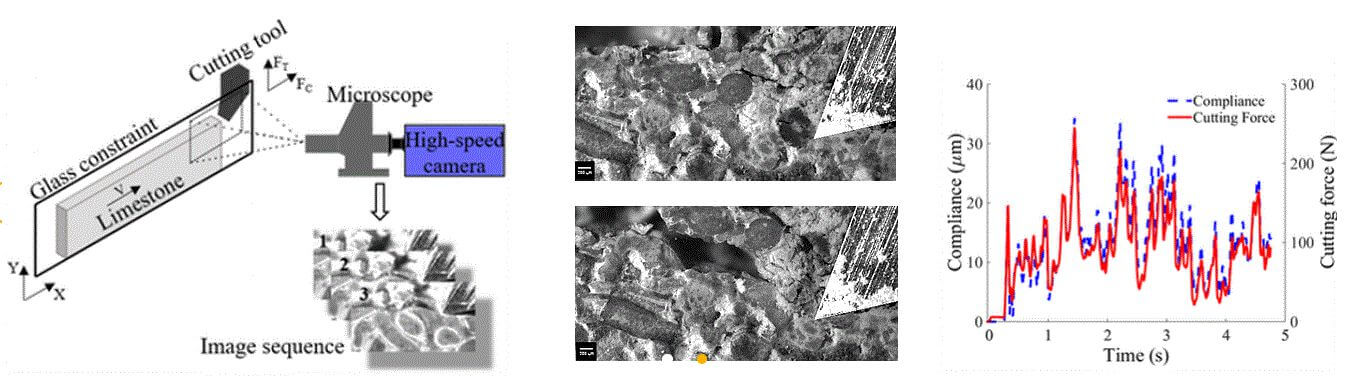
The chip formation process during the cutting of Indiana limestone is studied using high-speed in situ imaging. Synchronized imaging and force measurements are used to explain the observed differences in the cutting force fluctuations during a cutting cycle at low and high depth of cuts in the context of the various chip formation events. The high-speed images show that coarse chip formation occurs primarily through intra-granular fracture at low depth of cut and through inter-granular fracture at high depth of cuts. Cutting force measurements performed on two limestones with similar mechanical properties but different grain sizes show that the forces required to cut at a given depth are lower for rocks with larger grain sizes. Post-mortem analysis of the cutting chips reveals that brittle fracture is the dominant cutting mechanism across all the studied depths. Nanoindentation tests are performed to characterize the critical ductile-brittle transition depth. Results reveal that ductile chip formation can occur in limestones only at very low depth of cuts (< 600 nm).
Status: Completed
Collaborators: Prof. S. Chandrasekar (Purdue University), Dr. H. Yeung (National Institute of Standards and Technology)